The Application of Defoamers in the Pulp and Paper Industry
The Application of Defoamers in the Pulp and Paper Industry
Blog Article
Discover the Top Advantages of Using Defoamers in Industrial Processes
The usage of defoamers in commercial processes offers an array of compelling advantages that can boost operational performance and product quality. By efficiently managing foam production, these representatives not only optimize material flow but likewise contribute to significant cost decreases and enhanced sustainability. Their application spans multiple markets, which questions concerning their role in mitigating ecological impact while making certain consistent outcome. Understanding these benefits is essential for sectors aiming to fine-tune their procedures. The implications of embracing defoamers might be more profound than originally perceived. What particular advantages could your company harness?
Boosted Process Efficiency
Enhancing commercial procedures often involves dealing with lathering concerns, which can prevent functional efficiency. Foam formation can interfere with the appropriate performance of equipment, decrease the effective use of sources, and make complex the surveillance of critical parameters. By implementing defoamers, industries can successfully reduce these issues, leading to streamlined procedures and boosted efficiency.
Defoamers work by destabilizing the foam structure, permitting rapid collapse and substantial decrease in foam volume. This action not just boosts the circulation of materials through tools, such as activators, pipes, and mixers, but additionally decreases disturbances triggered by foam overflow. As a result, equipment downtime is lowered, permitting a much more reliable and continual manufacturing procedure.
Furthermore, using defoamers can cause decreased power usage. With much less foam to handle, pumps and compressors can run much more successfully, leading to reduced operational expenses and a general renovation in process throughput. Inevitably, the calculated use of defoamers not only addresses prompt frothing difficulties but likewise adds to a much more reliable industrial ecosystem, promoting an affordable advantage in a requiring market.
Improved Item Quality
The assimilation of defoamers in industrial processes plays a crucial function in boosting product high quality. By properly controlling foam formation, defoamers add to the uniformity and uniformity of final products. Extreme foam can lead to aeration, which negatively affects the appearance and security of formulations, especially in markets such as food and drinks, drugs, and coverings.
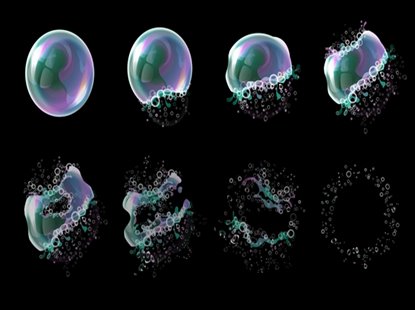
In addition, defoamers help with far better mixing and dispersion of ingredients, leading to homogeneity in solutions. This is crucial in applications where precise ingredient proportions are vital for performance and safety and security. Additionally, the removal of foam can reduce the risk of contamination during production, further guarding item stability.
Eventually, by boosting item top quality, defoamers not just improve consumer contentment yet also strengthen brand name credibility. Their function in keeping premium requirements emphasizes their relevance in modern-day commercial processes.
Cost Decrease Advantages
Applying defoamers in industrial processes can cause substantial price reduction advantages. By successfully regulating foam development, defoamers minimize item loss during production, thus maximizing product use. This decrease in waste equates straight right into reduced basic material prices, boosting total operational effectiveness.
Additionally, making use of defoamers can decrease power intake. Too much foam can prevent devices performance, leading to boosted power demands to preserve production levels. By minimizing foam, defoamers help with smoother procedures, permitting machinery to run a lot more efficiently and decreasing energy expenses.

Additionally, defoamers can reduce handling times. Foam can create additional challenges that lengthen production cycles. By utilizing defoamers, markets can streamline their procedures, resulting in faster turn-around times and boosted throughput. This efficiency not just accelerates manufacturing however additionally enables firms to satisfy market needs much more swiftly.
Environmental Impact Mitigation
In commercial procedures, using defoamers plays an important function in mitigating ecological effects related to foam generation. Foam can bring about considerable functional inefficiencies, resulting in boosted emissions and waste generation. By properly controlling foam, defoamers help maintain procedure effectiveness, therefore reducing the general environmental footprint of operations.
Furthermore, excessive foam can overflow control systems, bring about spills that may infect dirt and water resources. Defoamers aid minimize this danger by ensuring that lathering does not surpass suggested limits, promoting conformity with environmental policies. This aggressive strategy not only safeguards ecosystems yet additionally enhances the sustainability of commercial methods.
Furthermore, using defoamers can reduce energy consumption in various processes. defoamers. Lowering foam development decreases the need for additional energy-intensive actions, such as boosted agitation or pumping, which may or else be needed to take care of foam. The adoption of defoamers straightens with broader sustainability objectives by promoting energy effectiveness while minimizing the carbon footprint of industrial tasks.
Eventually, integrating defoamers right into commercial procedures is a calculated step that sustains environmental stewardship and liable source monitoring.
Flexibility Throughout Industries
Across different markets, defoamers demonstrate exceptional convenience, adjusting to the certain requirements of diverse applications. In the food and drink field, for example, defoamers are important to maintaining product quality by avoiding foam development during processing, which can affect structure and taste. Likewise, in the pharmaceutical market, defoamers make certain the security of formulas, enhancing item effectiveness and consistency.
In the chemical production world, defoamers assist in smoother operations by minimizing foam in reaction vessels, therefore improving return and lowering downtime. The paper and pulp market counts on defoamers to enhance the performance of pulp processing and paper production, making certain optimal item honesty. In addition, in wastewater therapy centers, defoamers play a crucial duty in managing foam throughout aeration processes, bring about enhanced treatment end results.
The versatility of defoamers includes the oil and gas industry, where they assist in taking care of foam in drilling liquids and manufacturing processes. By tailoring formulations to satisfy particular industry needs, defoamers act as indispensable devices that improve operational efficiency, item quality, and total procedure efficiency across a wide variety of industries. Their versatility emphasizes their value in contemporary commercial applications.
Final Thought
To conclude, the usage of defoamers in industrial procedures provides many advantages, consisting of improved efficiency, boosted product top quality, significant expense decreases, and positive environmental effects. Their capability to efficiently manage foam formation contributes to operational connection and source optimization. The flexibility of defoamers across diverse industries underscores their vital function in promoting lasting practices and profitability. The combination of defoamers represents a strategic technique to resolving difficulties related to foam monitoring in various manufacturing atmospheres.
Ultimately, the calculated use of defoamers not only addresses instant lathering challenges but likewise adds to an extra effective industrial ecosystem, fostering an affordable advantage in a demanding market.
In industrial procedures, the usage of defoamers plays an essential her explanation function in mitigating that site environmental influences connected with foam generation. By efficiently controlling foam, defoamers help maintain process efficiency, consequently reducing the overall ecological footprint of procedures.
Furthermore, in wastewater treatment facilities, defoamers play a vital role in regulating foam during oygenation procedures, leading to improved therapy outcomes.
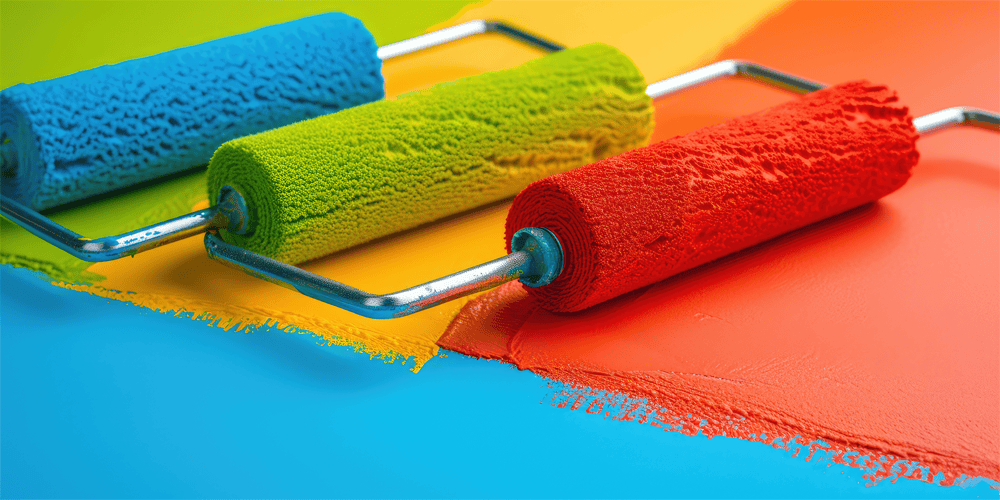
Report this page